Capabilities | Engineering
Alliance engineers will interface with your design team in the early stages of product development to provide the best solutions for product integrity and efficient and economic manufacturing.
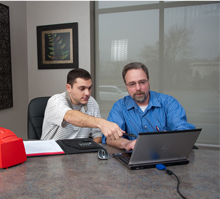
Cross-Functional Team Approach
Our engineering, tool design, process development, and quality control experts work together from the concept stage to ensure that the project is optimized for efficiency and long-term success. This collaborative culture is maintained throughout operations. Alliance embraces customers and suppliers as partners in the execution of this defect-free design approach.
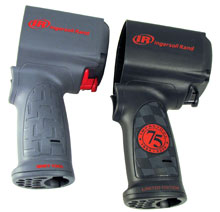
Molded Component Design Collaboration/Net Shape Design Consolidation
In addition to being strong, economical, and flexible, plastic parts can be designed to assimilate other parts into one component. For example, a plastic drill housing having receptacles for switches, clips and wire harnesses previously made of metals as separate parts, can be designed to have these parts molded as integral parts of the main component. Instead of multiple parts and added assembly time, customers get one streamlined plastic component with no assembly or finishing required. It's the smart way to engineer plastic products.
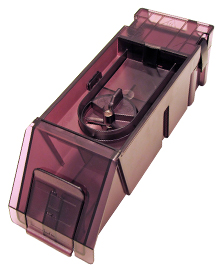
In-house Mold Design and Flow Analysis
Flow analysis speeds mold development by eliminating time-consuming trial and error processes. The end result is accurate, economical and reliable plastic parts. With the aid of flow analysis, our engineers obtain statistical data of the molding process before the mold is constructed. The object is to optimize the fill process of a mold and the integrity of the part. The data provided during the analysis helps our engineers select the optimum location for vent lines, gate position and feed system. Temperature variations, hot spots and potential stress points are clearly defined in the simulation.
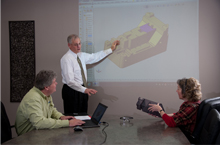
Material Selection/Metal-to-Plastic Conversion Assistance
Since the introduction of high-impact, engineering grades of thermoplastics, components that were typically made from metals are being widely replaced. Lighter weight, flexibility, color-ability, corrosion resistance and lower costs are just a few of the reasons the use of thermoplastics in component manufacturing is on the rise.
The continual development of advanced engineered composites is stretching plastics' physical properties, and advancements in controlled processing operations and technology are resulting in significantly improved performance.